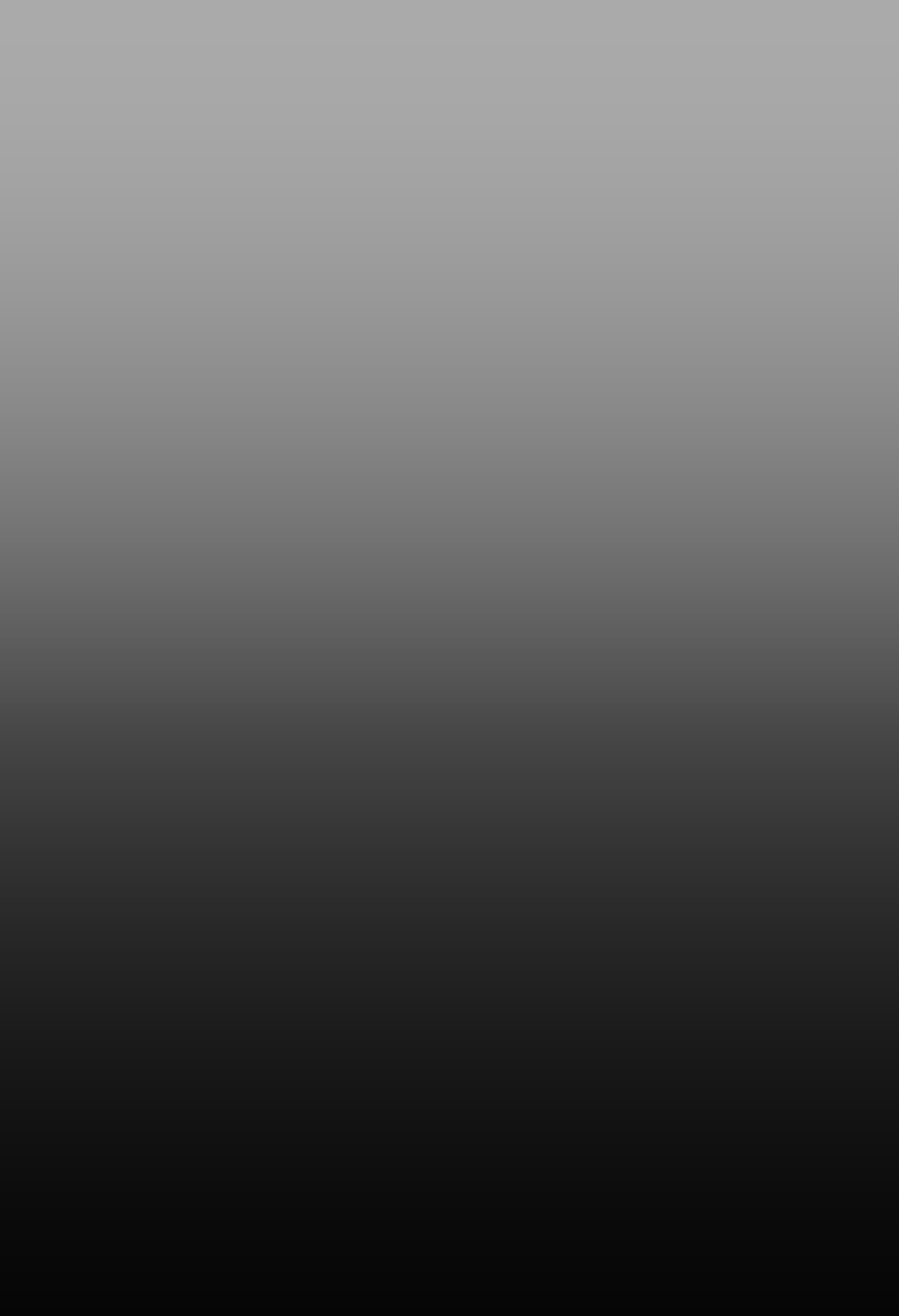
KIMONO REBORN
Project Team, Who We are.
We are initially video
production team.
KIMONO REBORN is a social business project of K.M.Tomyam Co.Ltd., a video production company in Thailand which was founded in 2005 by Yasuhiko Okuno, a Japanese documentary photographer and a video producer.

Leelaa, a presenter of KIMONO REBORN with elephants. We got many unecpected beautiful stories during the filming. Our team also worked hard for the clothes and digital media productions.
We have produced several travel programs about Japan for Thai TV, and more recently, for NHK World, an English-language channel of Japan’s National broadcasting organization. We feature documentary with some aspect of sustainability.
We have also initiated “TENKAWA”, a Thai high school students’ photo contest since 2014, one of our CSR activity in collaboration with Higashikawa Town in Hokkaido, Japan.

The KIMONO REBORN project is directed by Mieko Saho, Yasuhiko’s partner. All video, photography and digital content are managed by our team. However, the project could not have been possible without the support of Save Elephant Foundation, Elephant Nature Park and our friends in both Japan and Thailand.

Mieko Saho, Director of KIMONO REBORN project
Mieko was born in Japan and studied French literature in university in TOKYO, and went abroad for a year in France. Her experience there opened her eyes to cross-cultural issues. After working for a fashion magazine in the early of 1980’s, she moved to a media production company where she trained to become a journalist.

As an independent reporter, she has covered social, cultural and human stories in South Africa for several Japanese magazines and newspapers with Yasuhiko, her business partner and husband. In 1994 she published her first book which documented the life of a white South African woman who married a black man under the apartheid regime.
In 2004, while raising her two children, she published another book which depicted the life story of a Japanese woman who founded a children’s home for HIV affected infants in Thailand.
Mieko and Yasuhiko have supported them through their media and volunteer work. The field research trips for the book connected her and her family to Chiang Mai. That year, they decided to move to Chiang Mai to begin a new chapter in their life journey. Yasuhiko set up K.M.Tomyam, a video production company, and Mieko has been supporting their works. She is a nature and animal lover and very interested in the circular economy. The KIMONO REBORN project has been inspired from her work experiences and life journey overseas.
KIMONO REBORN
work process below


KIMONO REBORN Work Process
How does kimono “REBORN” into a modern fashion garment?
Transforming a vintage kimono into a modern fashion garment requires a different process from the usual dress making. The biggest difference is to prepare the valuable fabric before sewing, which must be done by hand. The priority must be to maintain the quality of the kimono fabric.
For example, one kimono can produce one unique kimono jacket. Since our material is limited and already cut into 8 pieces from a single bolt of 36cm width cloth, the design must be created with these challenging conditions. Each KIMONO REBORN jacket is unique, so the design pattern must be size, age, and gender inclusive. In this way, the neglected vintage kimono can be “REBORN” into a modern item that is fun to wear for a wide range of customers.
“No Waste” is a core value of KIMONO REBORN.
Even though upcycling vintage kimono is a practice of “Mottainai, Do not waste!”, we always maximize the use of kimono-material after removing the damaged parts of the fabrics (stains, fading of color, etc.)
The left-over fabrics will be fully used for other products like vests, scarfs, shipping bags and fabric accessories. No-waste is not only to take care our mother nature, but also to respect the artisanal works of the original kimono.

Our shipping bag, made of Kimono liner,is reusable.

scarfs, made of the left-over fabric and kimono liner.